Boat construction and materials have come a long way since ancient mariners first hollowed out a fallen tree and floated downstream. Many of us remember the early builds from Hatteras — think back to the 1960 introduction of Knit Wits; at 41 feet in length, it is considered to be the first fiberglass production boat over 30 feet, and one that is still running to this day. But did you know that the use of composite materials dates back to antiquity?
In the Beginning
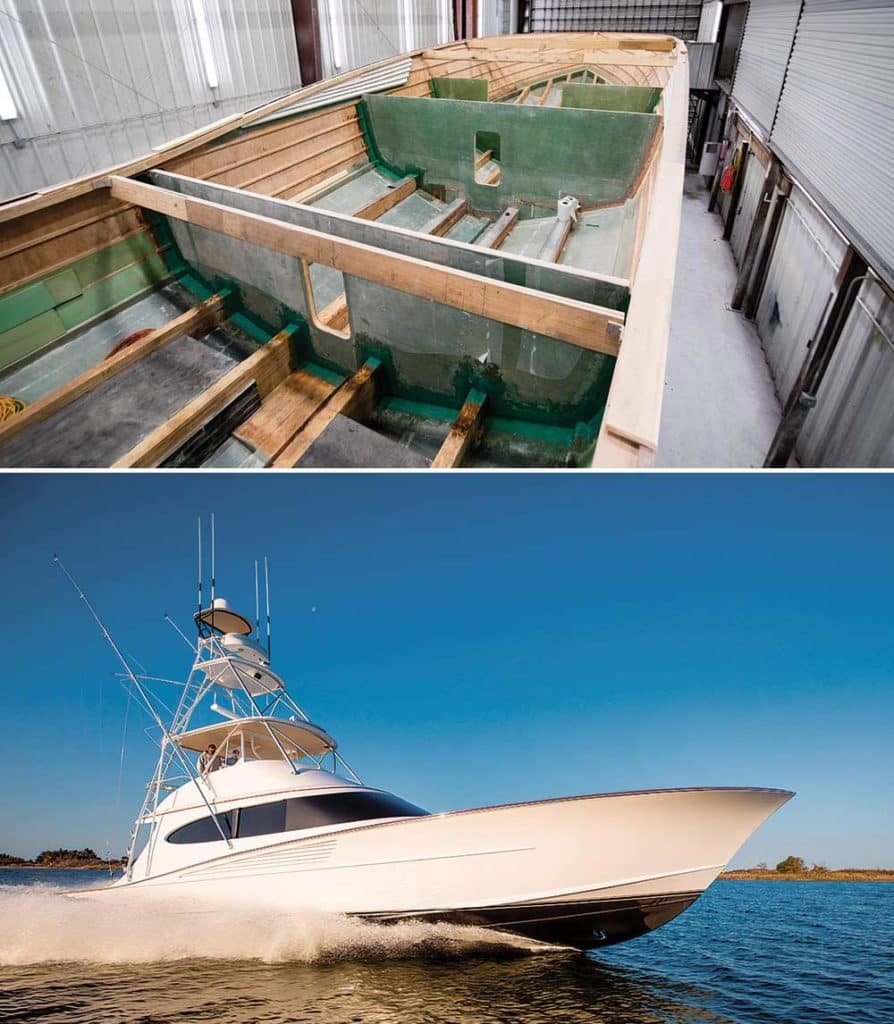
According to scholarly research, the earliest record of composite use is generally attributed to the ancient Mesopotamians around 3400 B.C. Using their own homegrown sticky stuff, they glued strips of wood placed at different angles to one another, and voilà: plywood was born.
The use of composites grew by leaps and bounds, and by around A.D. 1200, those rascally Mongols figured out that by using a combination of wood, bamboo, animal tendons and bones, all wrapped in silk and bonded together with pine resin, their bows were much more effective. So effective, in fact, that the weapon ruled their world in both hunting and warfare well into the 14th century, when firearms first appeared.
Fast-forward to the 1930s, when resin development took a giant step forward, paralleling the introduction of fiberglass by the Owens Corning company. Fiberglass-reinforced polymer was given a patent, and it would only be a matter of time until the automobile industry designed and produced a totally composite car body. After the introduction of the 1953 Corvette, the marine industry caught on.
In the next decade and onward — with the patent of carbon-fiber material for commercial use, technologically advanced resins and epoxies, new fabric weaves, better strength-to-weight ratios and the advent of Everett Pearson’s Seemann Composites Resin Infusion Molding Process (SCRIMP) system of vacuum bagging — other innovations have brought us right up to today’s high-tech, state-of-the-art construction methods, ones that have given us some of the most beautifully built and functional fishing machines known worldwide.
To get a handle on just how all this has affected high-level tournament-ready sport-fishing boats from the custom sector, I went right to the source with several well-known builders to get their input.
A Flair for Innovation
“We put a lot of engineering into our boats, and each one, from a 60-footer to a 90-footer, gets the same attention,” says Gary Davis, superintendent of new construction at the sprawling Jarrett Bay Boatworks facility in Beaufort, North Carolina. “You can’t just add more horsepower to make the boat go faster. The only way to skin that cat is to look for ways to improve the hydrodynamics and eliminate weight. Those are the challenges that new technology addresses.”
We put a lot of engineering into our boats, and each one, from a 60-footer to a 90-footer, gets the same attention.
The Jarrett Bay approach looks at the whole build to ensure all of the critical structural parts, as well as all of the boat’s systems, work in harmony in order to exceed expectations. “For example, with our 90-footer, the owner wanted the boat to be not just fast but as quiet as possible,” Davis says.
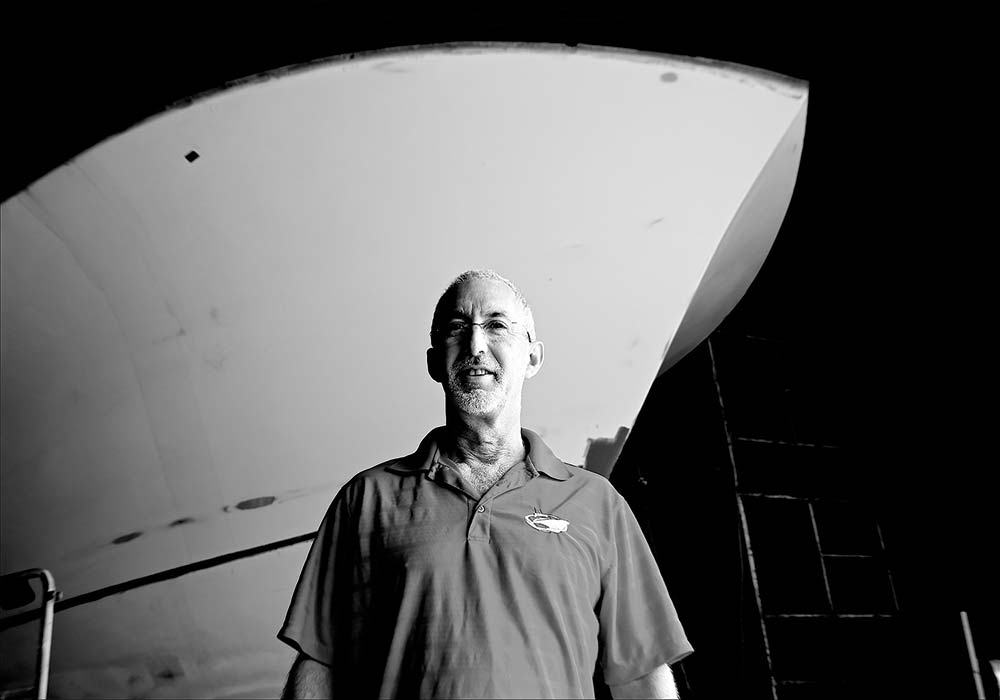
With the research done, they determined that while a full carbon-fiber package would yield the best speed, with the level of sound-dampening material needed to achieve the desired decibel levels, the weight savings would be eliminated, and the boat would actually be heavier. “We came up with a hybrid method for the hull skin, sides and transom by building them out of the relatively same lightweight material we have been using over the past 15 years — a cold-molded product made out of plywood and epoxy,” Davis notes. “The wood acts as a fairly good sound insulator too.”
After that, the similarities go away. For example, all the stringers, bulkheads, decks and everything from there on are foam-cored, with carbon-fiber-infused skins. “In the case of all the topside stuff, we’ve taken the E-glass out and replaced it with carbon fiber,” Davis says. “On the hull itself, we do have the E-glass laminate on the hull, inside and out, but after that, and with a few exceptions, everything else is a carbon-infused lamination.”

Carbon, research and manufacturing for the production of cars and aircraft
As far as mounting those new high-horsepower engines, one of the headaches with carbon fiber is the absolute need to isolate it from metals to prevent galvanic corrosion. The main stringers where the engines sit have a higher-density foam core and an overlay of carbon fiber. Over that is a welded aluminum cap that is properly sized to accept the motor mounts. To isolate it all, a layer of E-glass was applied before the paint. And to make sure the through-bolts would not come in contact with the carbon fiber, a compression sleeve was inserted. “Everything you see mounted on that boat, and everywhere that particular material is used across the board, we use a compression or grip sleeve to make sure there is no chance of any contact with a screw, bolt or metal component to set up galvanic corrosion,” Davis says. “This does complicate the build, but we made it happen.”
With the blessings of technology and new materials come a host of ills that must be addressed. “With the new processes, we are always looking for weight-saving opportunities, and in the final analysis, it all adds up. To make it happen, everybody involved has to be in the same mindset,” he adds.
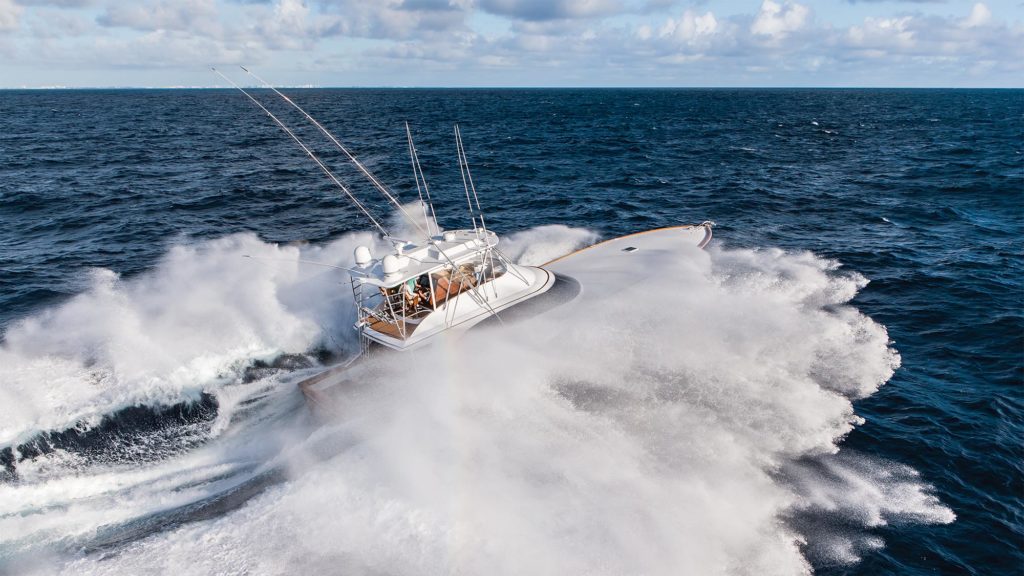
The Bayliss View
“We are big believers in the triple-ply Okoume hull, and I think, universally, everyone can agree that nothing compares to the sound-deadening capability, the ride and the performance of this hull,” says John Bayliss, whose boatbuilding facility in Wanchese, North Carolina, bears his name.
While the hulls at Bayliss Boatworks are glass inside and out, and use epoxy resin throughout the build, the construction process will vary with the building materials used. During wood construction, for example, a specific West System epoxy will be applied. “When we get to the cabin, superstructure, flybridge and console, we use Core-Cell foam that is glassed on both sides,” Bayliss notes. “We still use Philippine mahogany for the framework in the overhead of the cabin, which provides room for air ducts, wiring bundles, lighting and so on.”
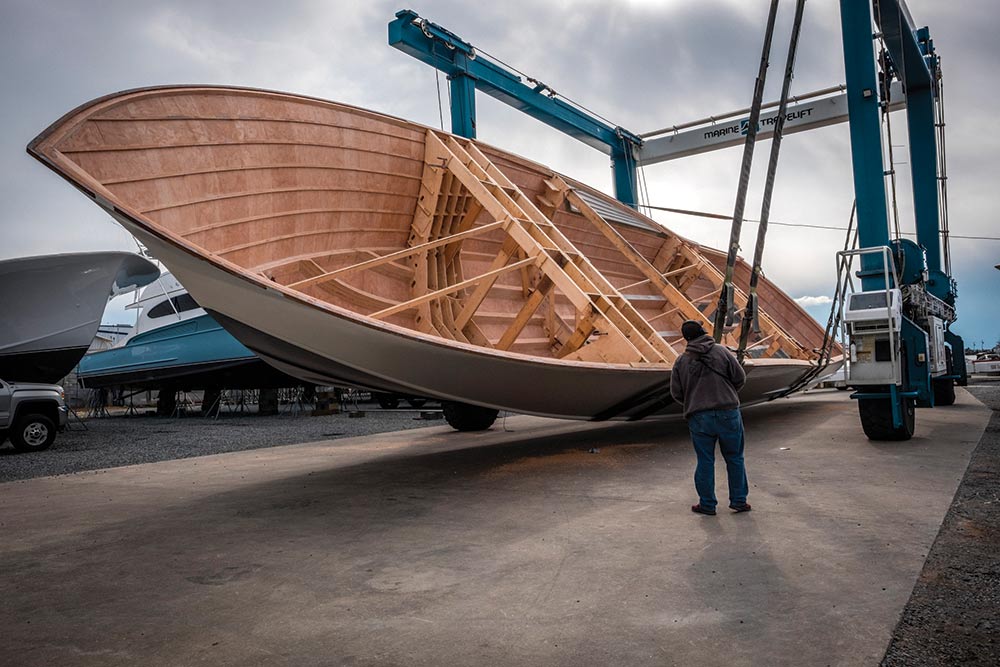
Bayliss and I discussed the all-important notion of being weight-conscious throughout his builds. While that is essential in today’s horizon-chasing fishing boats, his personal stamp on every boat that leaves the facility also comes with a pedigree that pays special attention to the ride. “I believe there is such thing as getting too light and high-tech, where a solid glass or core boat tends to resonate the sound more. That’s why we stick with cold-molding and the wood hull,” he says.
Learn more about The Anatomy of a Modern Sport-Fisher.
To further weight savings, Bayliss has replaced his decking material with a very durable 3M honeycomb core, and all bulkheads are a combination of marine plywood and Core-Cell, glassed on both sides. “Our boats are really quiet, ride very well and fish like they are expected to,” he says. “As far as all these new materials are concerned, and while we’ve adopted some of them into our builds and construction process, like CNC [computer numerical control], in-house design and the use of carbon fiber in certain areas for stiffening, we like to think that we have the kind of consistency to keep doing things the way we’ve always done them.”
Spencer’s Take on Tech
“We’ve been on the forefront of new technology for some 18 years now, with resin infusion, composite construction, Core-Cell, Divinycell and incorporating carbon fiber,” says Paul Spencer, of the Wanchese, North Carolina-based Spencer Yachts. “And we’re always looking for new ways to make things lighter and stronger on our boats.”
We’ve been on the forefront of new technology for some 18 years now, with resin infusion, composite construction, Core-Cell, Divinycell and incorporating carbon fiber.
The formula of horsepower plus weight equals speed and performance is the well-accepted math for serious sport-fishing boats, and while Spencer and the other builders seek to push the limits of their builds, they all must keep something very important in mind: The boat must still withstand the rigors it will be put through at sea.
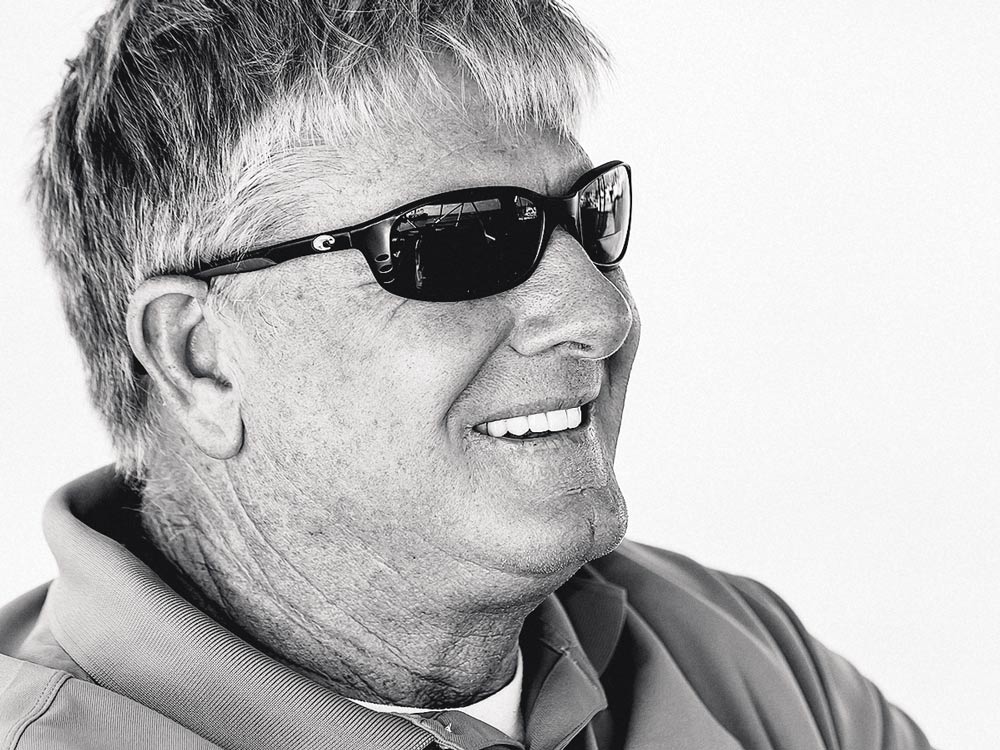
To that end, when Spencer first began with composite construction, the company engaged structural engineers to supply most of the data. In addition, with the all-important resin companies, the builder also consulted on which were the best formulas to use for resin infusion, given the higher temperatures. “We use post-curing for our builds, and will actually cook the whole hull, cabin and bridge in an autoclave oven in order to gain the full benefit of the product,” Spencer says. “When we cure at 200 to 250 degrees, the result is a harder, more stable outcome, without any of the post-cure issues like print-through. This way, we are able to take full advantage of these high-tech resins.”
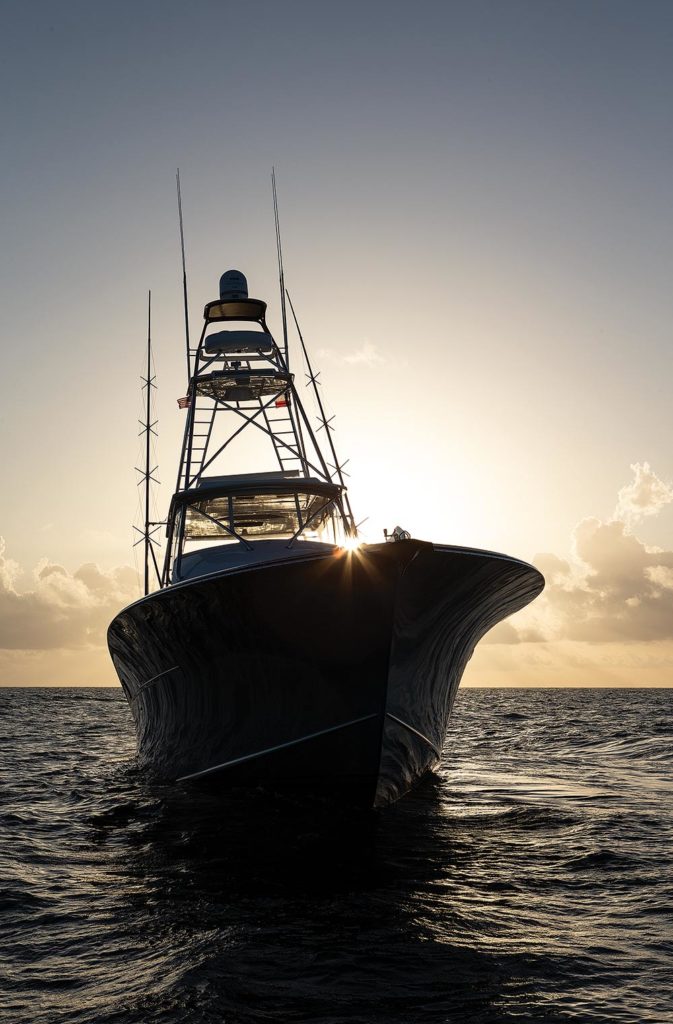
When it comes to carbon fiber, Spencer notes a lot of good uses for the material. “In our bulkheads, for example, it’s great because it won’t be abused there,” he says. And while carbon fiber does have its drawbacks — the aforementioned need for isolation, for example — there are many other uses where strength and weight savings are needed. “We don’t do the hull, but with the bulkheads and decks where you would need, let’s say, 20 ounces of E-glass, it only takes 10 ounces of carbon fiber and half the amount of resin to saturate it,” he points out. “The weight savings can be significant.”
Spencer’s main focus is its continued use of composites in a jig-built boat —incorporating any new technologies that can strengthen its builds and make them lighter — after strenuous research and testing, of course. For this builder, it’s not any one thing but a series of innovations that result in the boats you see coming from their facility.
Willis Owns His Turf
Building with high-tech materials is where Mark Willis’ Stuart, Florida-based Willis Marine finds its comfort zone. “From the initial conversation with the customer, we know right from the start whether it’s going to be a high-tech build or something a bit more mainstream,” he says. “And it doesn’t matter whether it’s one of our custom flats boats or a complicated build like the 77-foot Uno Mas, we approach everything in the same way.”
In order to get things going, Willis and his team start with computer studies and a full CFD (computational fluid dynamics) analysis, which shows the characteristics of an object as it interacts with water. Along with weight studies, this allows Willis to develop an idea on paper of what the best build platform is, way before any construction begins.
Anybody who wants Willis Marine to build them a boat wants something that sets them apart from the others. I’m always looking for that particular challenge.
“While the design process remains the same, using materials like carbon fiber will affect the weight studies since they are significantly lighter than the traditional glass composite or wood structure,” Willis says. “When we go this way, tracking the weights during every phase of the build becomes an integral part of the plan.”
With a somewhat visionary approach, Willis is also taking a new slant when addressing the running gear on his boats. And while the technology has been around for some time, having roots in the military, the weight-adapted methodology considers the struts, shaft, props and rudders as one system — what Willis calls an engineered drivetrain. “They are analyzed through CFD to be as slippery as possible, given the weight of the water passing through and by them,” he says. “It’s this kind of stuff that is bringing the marine industry well into the 21st century.”
Willis and I discussed the approach he used for Uno Mas, working with an owner who came to them with a cutting-edge idea that would push the envelope right from the start. “We really worked on the styling for many months, using models and 3D computer programs, until everyone was happy with how it was going to look,” he says.
Willis is comfortable with his niche in the market and prefers to use high-tech materials in his builds. “For me, anybody who wants Willis Marine to build them a boat wants something that sets them apart from the others,” he says. “I’m always looking for that particular challenge.”
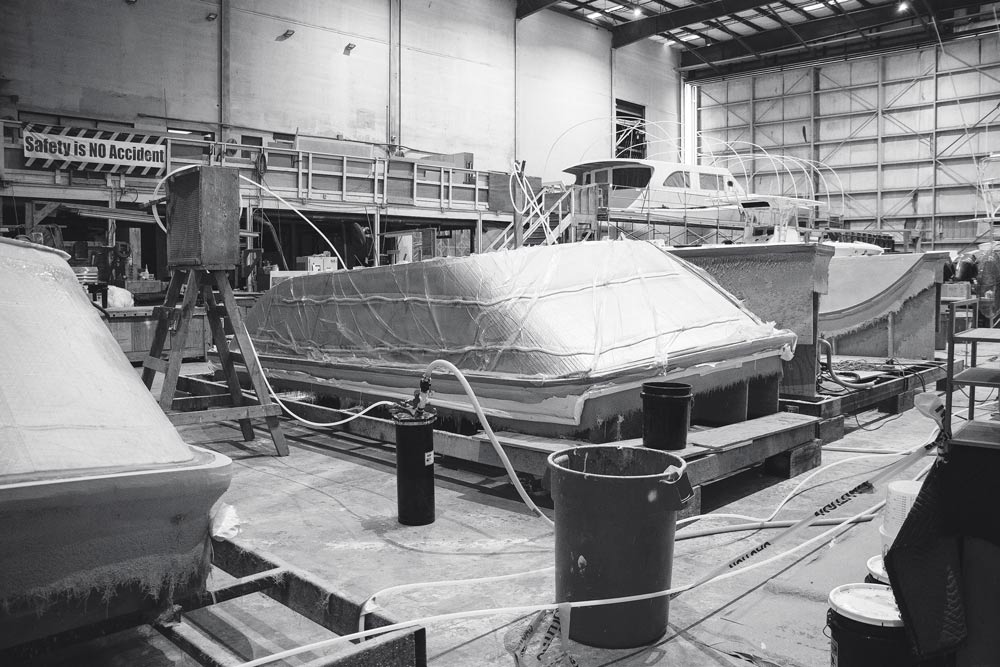
ACY and the Need for Speed
Dominick LaCombe likes to go fast, from his motorcycles and cars to the boats that slip down the ways at his American Custom Yachts facility in Stuart. “It’s all about the weight,” he points out. “Lighter means faster. We were building light, strong boats when the horsepower wasn’t there. When the engine horsepower started to get higher, our light, strong builds were already there performance-wise,” he says.
Back in the 1980s, LaCombe began using carbon fiber to reinforce the deck beams, as well as replacing the fiberglass fabric with Kevlar for added strength and reduced weight. “The Kevlar was really good for collision bulkheads,” he notes.
LaCombe’s take on working with carbon fiber echoes everyone else’s concern about the material: “Think about it as being a sheet of steel,” he says. “If you put a screw in it, you’re going to have to isolate those two metals.” And with that in mind, ACY makes absolutely sure that whenever carbon fiber is used, special attention is given to protection and isolation.
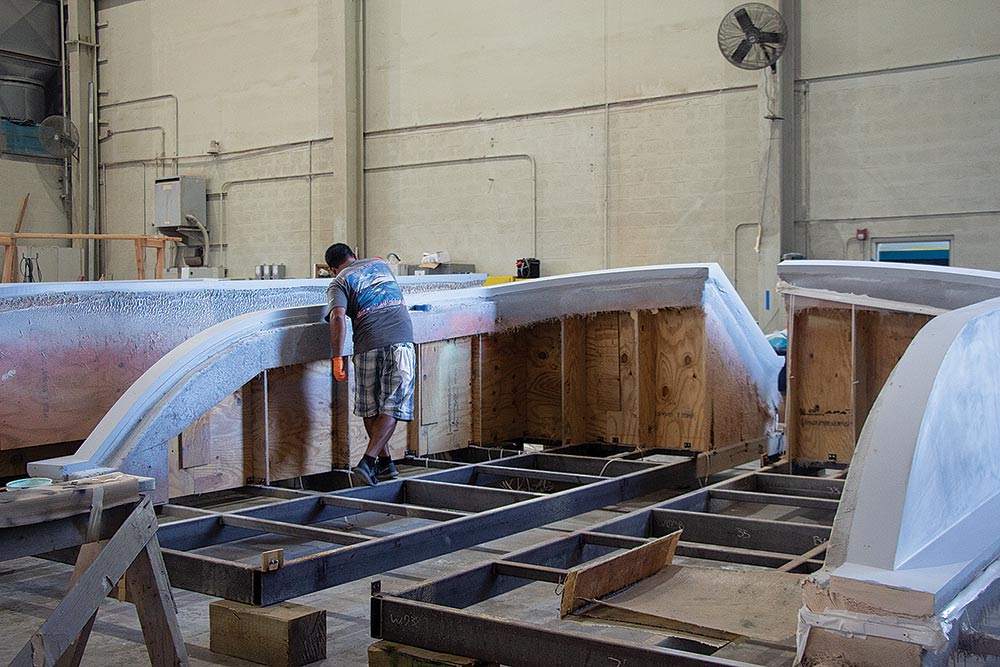
Being a custom builder, ACY uses limited production tooling molds for the house and flybridge; the former has Core-Cell foam beams in the overhead for the bridge deck. This is one of the places where they use vacuum-infused carbon fiber along with Pro-Set epoxies to prevent any print-through. “We own the whole infusion pump system and are able to make sure the resin-to-weight ratios are kept right where they belong,” he points out.
With technology delivering new resin chemistry, ACY has taken advantage of the advances by integrating the advanced formulas into its builds. Everything in the design and building process that technology has provided to make things a little bit lighter and more user-friendly, LaCombe says, has been incorporated into the boats that bear the ACY name.
Looking Ahead
As technology continues to advance, it will be interesting to see what comes down the line and how that will affect our industry and, in particular, the custom builders. There are radical designs already showing up, and new ideas about propulsion options and building materials that will see the next generation of boaters looking back at what came before, just as we do with the first fiberglass boats. Time will tell.