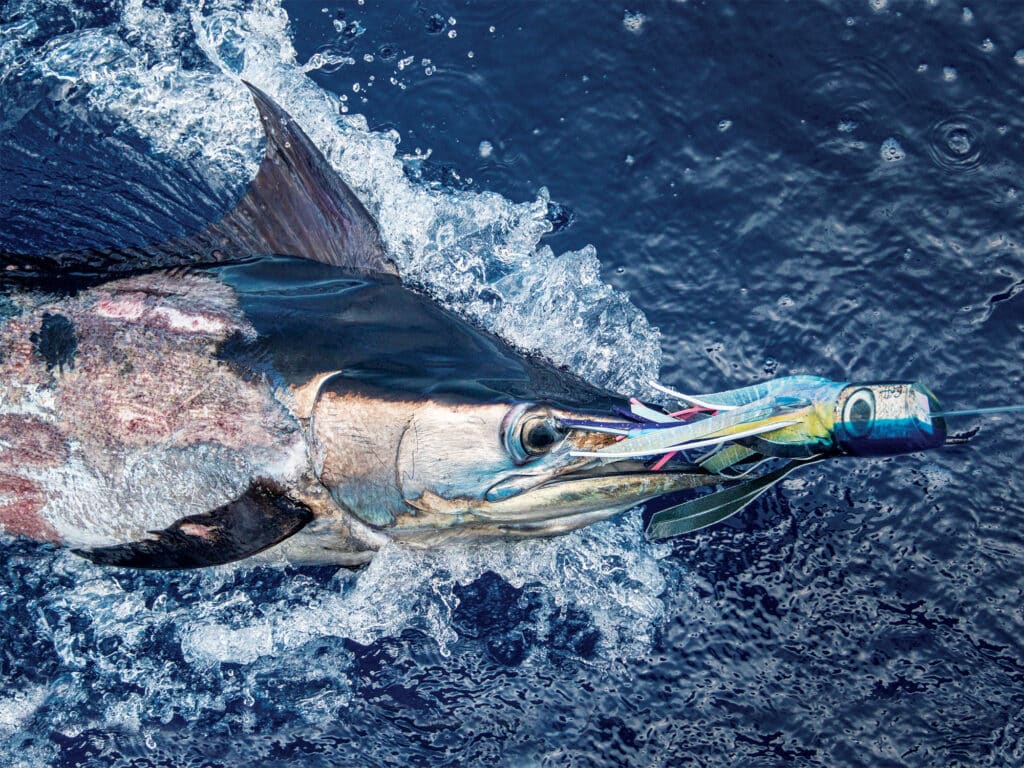
Special delivery: Sign up for the free Marlin email newsletter. Subscribe to Marlin magazine and get a year of highly collectible, keepsake editions – plus access to the digital edition and archives.
In Polynesian culture, and certainly on the islands of Hawaii, the concept of mana manifests itself across activities and conversations on a daily basis. The belief is that certain objects can hold energy, or even a sort of supernatural force—a sacred wisdom passed on to the object by its creator. This undercurrent of spirituality often influences or even overshadows the science or technique employed in any creative endeavor, and that holds true in the evolution of artificial lure design, of which Hawaii is known as an originator and innovator.
In Hawaii, lures are not called “plugs” or “plastics.” In fact, many consider it almost sacrilege to speak about them as just a piece of material. Here in Kona, they are “baits,” and they are treated with as much respect and care as one would give to the most expensive reel. We’re particular in how we store them, preserving the leader’s coil memory while the lure is not in use. It pains us to see these baits scattered about, coils all tangled or wrapped up tight, jammed into a bag, tossed around in a cubby, or hanging upside down from the reel or rod guides on the run to the fishing grounds.
Why? Other than the fact that they are our primary way of fishing for marlin here, it probably dates back to when primitive lures were used as a sacred tool to feed family and friends. As time went on and Hawaiians moved from carved bone or shell to the modern Chee-style trolling lure that was birthed in Hawaii, a sense of care and aloha was instilled in every bait. The old Hawaiian way of making these lures is time-consuming, an intimate practice taking hours of handling, sanding and perfecting.
While modern manufacturing techniques have increased production efficiency, and some would say have improved consistency among baits, the artisans that are driving modern advancements in lure design here in Hawaii still instill their baits with plenty of mana.
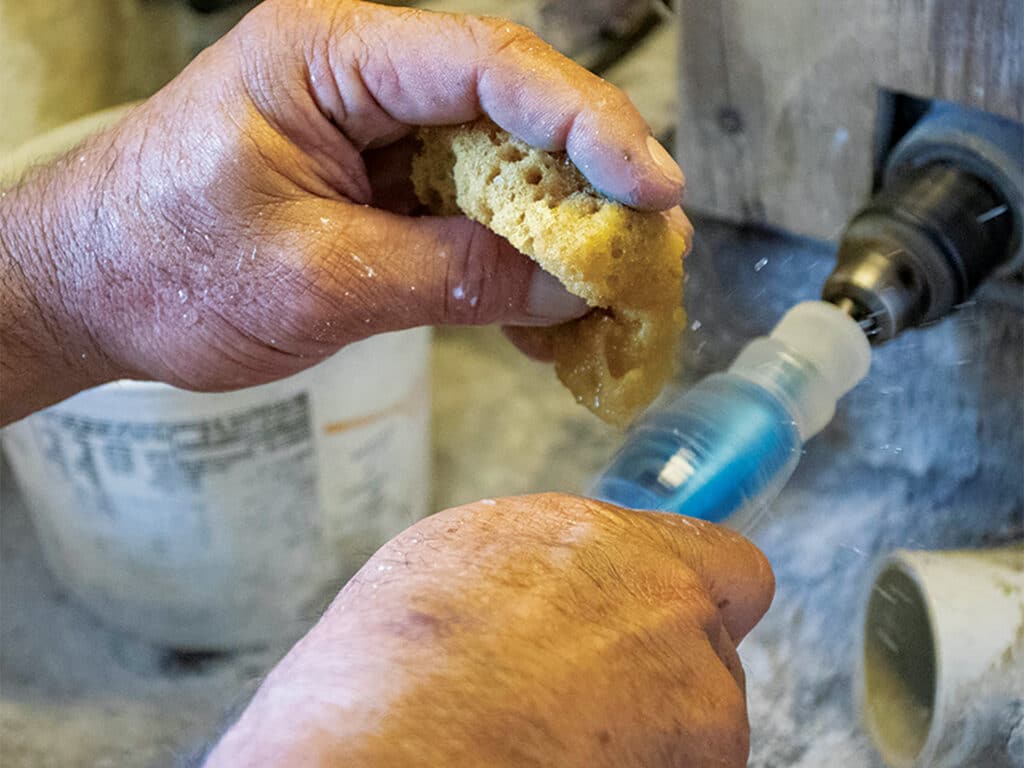
A Brief History
While ancient Polynesians deployed their own style of trolling lures through all of Oceania, the modern trolling lures we think of today were birthed in the quiet little town of Kona, on the western shore of the big island of Hawaii. The advancement of trolling lures went hand in hand with the advancement of trolling tactics and boat speeds. Most people in the early days were trolling from old wooden sampan boats that ran at much slower speeds, so scoop-faced and lead-head feather lures were the popular choice. They swam well at that slower speed, and this was how things remained until Capt. George Parker changed the industry in 1945.
With a simple twist of fate, Parker was walking past a renovation project for the Kona Inn and spotted some discarded scraps of chrome tubing. Like any true fisherman, his first instinct was to wonder if that material might help him catch more fish. He took the chrome tubing home and cut it into heads, making two at a time from a 6-inch piece of tubing. He put doweling inside and cut the heads on a shallow angle, with a diameter that varied between 1 ¼ and 1 ½ inches. He then skirted them with some furniture upholstery and red inner-tubing strips. What Parker fashioned out of that trash pile was truly revolutionary at the time.
His Hawaiian contemporaries laughed at him, but those laughs went silent when he returned with a 500-pound marlin on his first test run with his new lures. Later, he would catch Hawaii’s first documented grander, a 1,002-pound blue that succumbed to one of his homemade baits in November 1954.
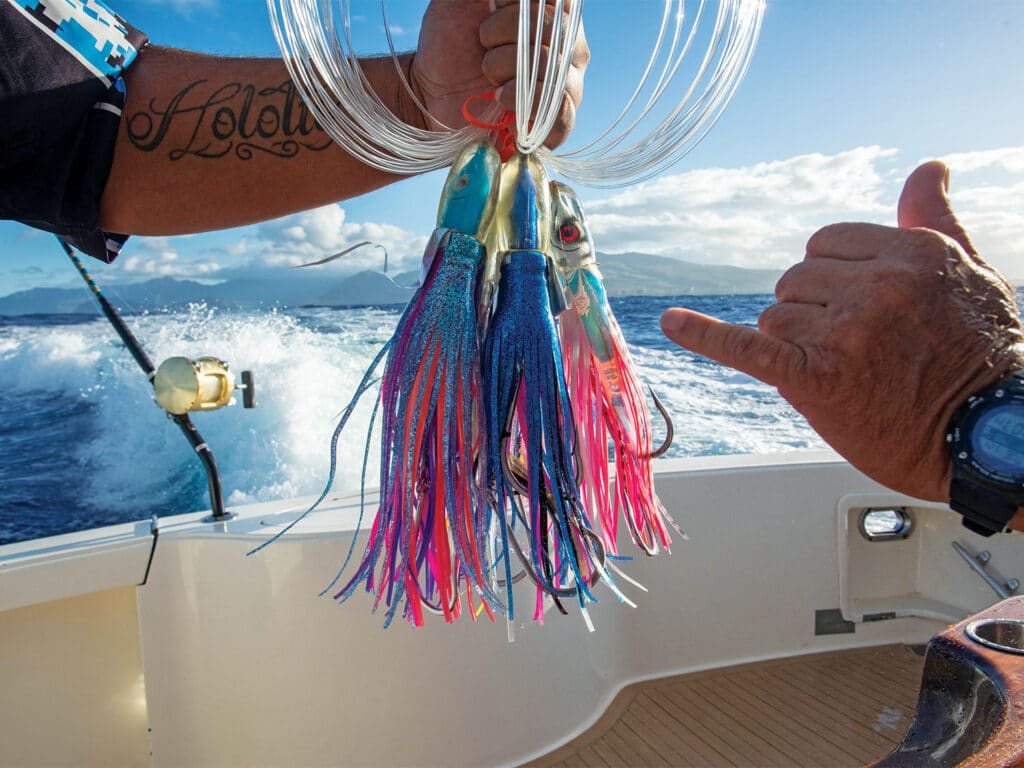
As Parker was on the water proving his lures’ effectiveness, legendary Capt. Henry Chee advanced trolling lure design further still. Like Parker, Chee was inspired by a trash pile at a local inn. Chee raised pigs on the big island to help cover expenses when not fishing. One day while collecting leftovers for pig feed from the Ocean View Inn, he noticed a screwdriver stuck in an olive jar full of hardened resin. Chee took one look at this and envisioned a metal leader tube instead of the screwdriver, with pearl shell and color additives included in the resin. Using the inn’s bar glasses, Chee poured his own resin heads. He developed two simple shapes—one was basically the bar glass with its taper, and the other a tube-style lure. These new baits caught fish and, fueled by global interest in Parker’s grander, sparked a billfish revolution.
Today, you can find countless variations in lure style, shape, bevel and inserts from dozens of manufacturers in your local tackle shop. But really, most of these designs originated out of Chee’s workshop decades ago.
Old vs. New
The old Hawaiian way of making lures featured a polyester resin similar to what’s used for making surfboards. This resin, when hardened and removed from the mold, needed to be hand-sanded and then polished, so each lure was handled by its maker from start to finish. This produced variation from lure to lure, illustrating why one bait might catch consistently and another ordered a year later can’t buy a bite.
More recently at lure manufacturing plants across the globe, improvements in technology, process and materials are driving advancements in modern lure production, bringing a more consistent product to the marketplace. Lures pop out of the mold with little to no sanding needed and just a bit of polishing required. The consistency of each and every bait is laser accurate, and the acrylic or polyurethane lure head is a lot less likely to break or chip. The lure aisle of your local tackle shop will be filled with these mass-market lures, and most of them will run great right out of the package and catch plenty of fish.
“I do think the old way of lure making is under threat due to advancements in technology, mass-market pricing and increased competition in the industry,” says Cole Miller, founder of GZ Tackle, an internet-based company that specializes in big-game tackle and fishing supplies. “Polyurethane lures are sometimes preferred because of their chip resistance and speed of production, which can result in a cheaper price.”
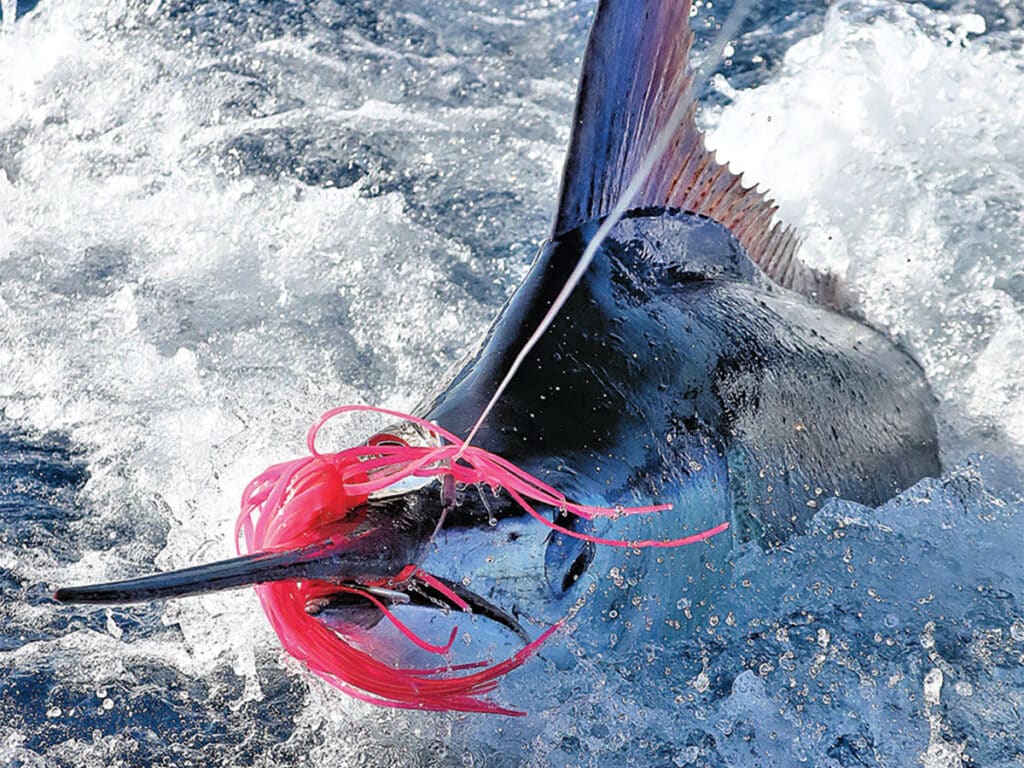
So how are Hawaii’s modern lure craftsmen managing the shift from old to new, from art to production? While many remain true to traditional ways, some local lure makers have embraced new tech, which allows them even greater focus on product creativity.
Dedicated to Their Craft
Eric Koyanagi, owner of Koya Lures based in Kona, still makes all his lures the old, traditional Hawaiian way, diligently hand-sanding each lure at his house. An advocate for incorporating feedback from fishermen in the harbor, Koyanagi frequently adjusts tapers, shapes or weights based on customer input, in nearly real time.
Chief among his early advancements was the introduction of a keel, or “belly weight,” to most of his slant-faced lures, as single-hook rigs began to replace the double hooks that helped balance the lure. He also experimented with eye placement, setting them far forward on some of the heads in homage to his mentor Joe Placate, who first developed that signature look. Some believe that particular eye placement gets the fish to strike more forward on the lure, allowing the hook a better puncture point.
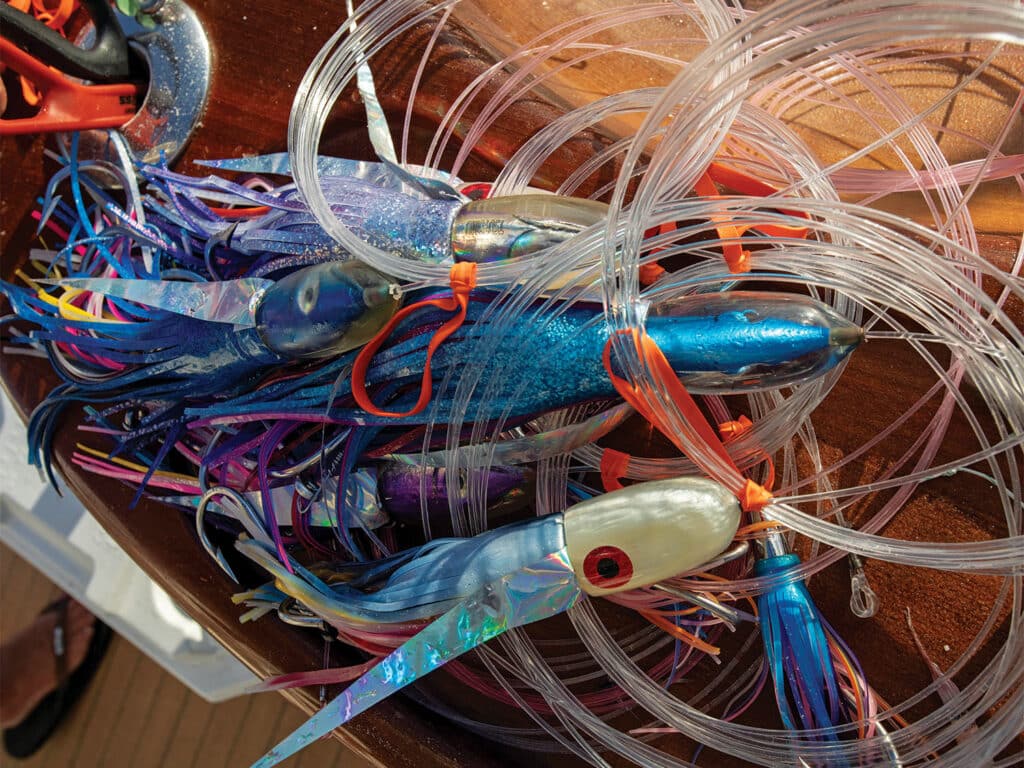
“People in the know still prefer handmade Hawaiian lures because of the artistic craftsmanship,” Koyanagi says. “And it affords me the ability to adjust the lure with cut or taper, which would be a lot harder to do with the newer acrylics.” Koyanagi acknowledges that overall demand for custom lures will diminish over time but envisions a day when handmade lures will be much more valuable, with prices to match.
Gary Eoff, who produces the famed Marlin Magic line of lures along with partner Marlin Parker, shares that sentiment. “We have tried the new materials, and we do use some of them, but we feel the old, traditional custom handcrafted lures are the way to go for us,” Eoff says.
Parker, son of lure originator George Parker, is acknowledged as one of the greatest Kona skippers ever and fishes his own lures just about every day. He experiments with advancements almost daily. As a result, Marlin Magic lures are quite possibly responsible for more tournament wins than any other handmade trolling lure. Its Ruckus lure shape was introduced in the mid-1980s and remains its most popular today. Other signature shapes include the Super Dog and the Ahi P. Eoff’s specialty is working with shell, which is highly valued by fishermen since it mimics the look of live bait.
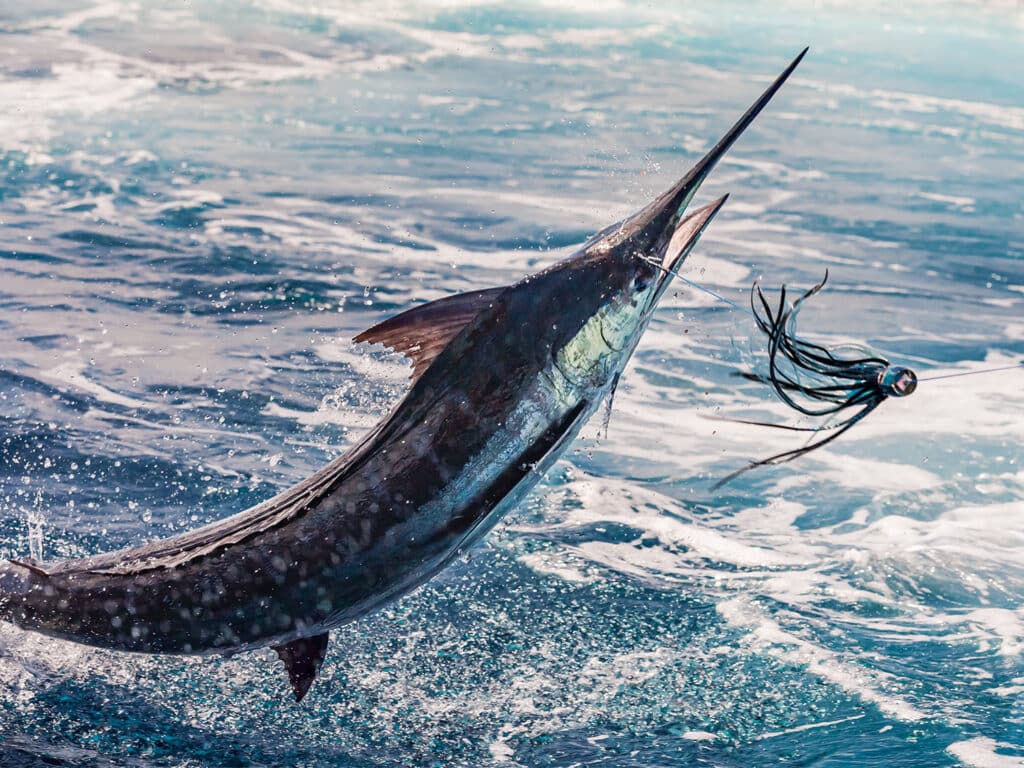
Embracing the Change
Before a lure can catch a fish, it must first catch the eye of a fisherman. As they embrace the time-saving benefits of new materials and processes, some Hawaiian lure makers have used that time to incorporate more creativity in their lure designs to grab the attention of potential customers. That has certainly been the approach taken by Erik Rusnak of Aloha Lures.
Rusnak spent many years pouring lures by hand before embracing technological advancements. Rusnak’s lures are absolutely legendary, catching giant fish all over the world for 40-plus years. He’s one of the few who has transitioned with the industry, and as he’s put more effort into his insert work, his business has grown tremendously.
“There is a mystical and secretive nature to the art and use of offshore trolling lures,” Rusnak says. “Any object dragged around in the ocean long enough will get eaten at some point, but fishermen invest time, energy, money and love into creating the perfect collection. Having an arsenal of trusted lure designs with proven results is mandatory preparation for serious bluewater hunters.”
Rusnak admits that it’s hard to beat the clarity and density of polyester resin, but after experimenting with acrylics, epoxies and polyurethanes, he’s settled on a mixture of materials and processes that eliminates most polishing needs. This was revolutionary for time saving and precise replication, but his financial investment in both resin and molds increased significantly. Molds need to be replaced fairly often, as they age and develop micro abrasions and surface damage.
“I’m always excited to see new creations and products that are only possible due to the new materials and information sharing that is happening today online,” Rusnak says. “Lure making is a combination of functionality, creative expression and composition. Whether you’re using new or old materials, there is no lure making without deep thought, experimentation, and inevitably, blood, sweat and tears.”
Another innovator on the scene in Hawaii is Jon Niiyama of Niiyama Lures, based in Oahu. Niiyama popularized the fish-head style of lure, using modern materials to craft lifelike fish heads, and started a whole new style of lure making in the process. “People like Jon have done a phenomenal job of proving that advancements in lure technology can allow for even more advancements in lure-making creativity,” says Miller.
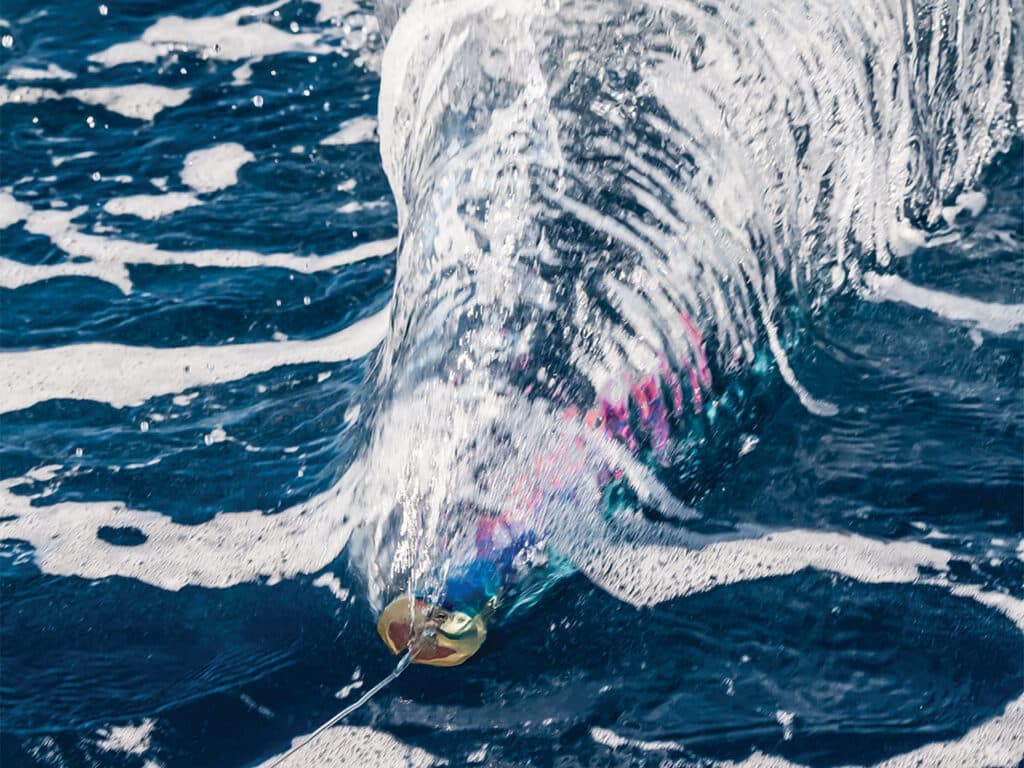
Niiyama says it took decades, and thousands of attempts, to perfect his fish-head style, which ultimately would be impossible to replicate reliably without embracing modern materials and techniques. “Advancements such as 3D printing, new materials, and the use of the internet in learning and sharing ideas allow us to be able to do things that were not possible even a few years ago,” he says.
While he produces all sorts of lures, Garrett Lee of Tsutomu Lures has come to specialize in baits built specifically to target ahi. That specialty, and the need to drive volume, led him to shift methods and materials.
Read Next: The Basics of Lure Fishing for Blue Marlin.
“My fishing focus has been giant yellowfin tuna, so I developed a bullet and an inverted shape to target them,” he says. “With that, our biggest challenge is manufacturing. Handcrafting lures one at a time at a high level takes skill, dedication and time. We have yet to crack the code of making enough lures to build a sufficient inventory to meet demand.”
Lee says technology is but another tool in the hands of a craftsman. “We are using both old and new types of resin, and both have their time and place. Lures made of urethane resins that you technically don’t need to sand still need some work after demolding if you want them to have all the luster and shine of the old polyester resins. It took us a couple years to figure out the process of using it for our particular style of lures.”
Like all other facets of life, the internet and social media are having a profound impact on Hawaii’s lure makers, not only changing the way business is conducted, but increasing design creativity as well. “The world is at your fingertips now,” Niiyama says. “It has allowed new and old ideas to emerge or reemerge, and there has been an explosion of creativity as a result.”
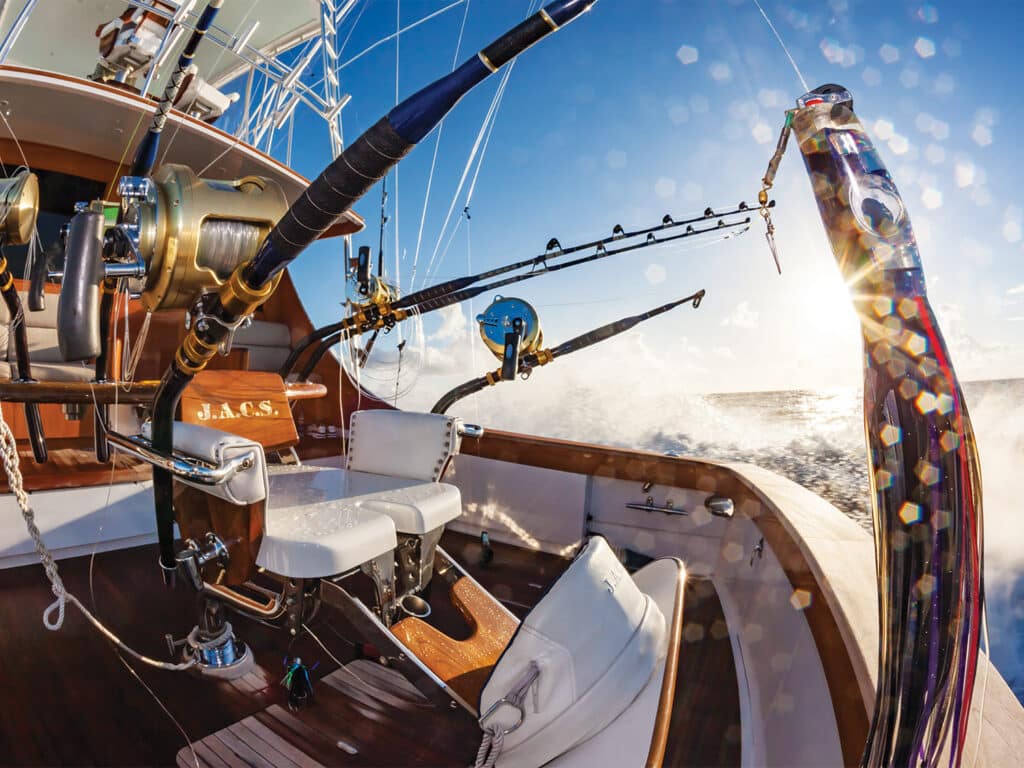
Business Is Booming
One consistent theme among Hawaii’s lure makers is respect for their peers, whether they be legends and mentors, or new craftsmen coming onto the scene. “The biggest trend I see is the boom of new lure makers entering the industry,” says Miller. “It’s awesome to see more fishermen getting into the business, driving progress in the art of lure making.”
“The evolution of materials and techniques has led to more competition in the market,” Eoff acknowledges. “My advice to new lure makers is to not simply change an established shape a few percentage points and call it your own. Be creative, make new shapes and looks, and contribute something new to the world of trolling lures.”
Regardless of a lure maker’s material of choice or preferred process, Miller expects that there will always be room for artistry in the spread. “There will always be a market for traditional hand-poured lures,” he says. “Whether it’s due to artistic appreciation or believing they perform better when it matters most, there is an aura to lure making that makes it special. People are willing to pay for a high-quality handmade lure. I don’t see that ever changing.”
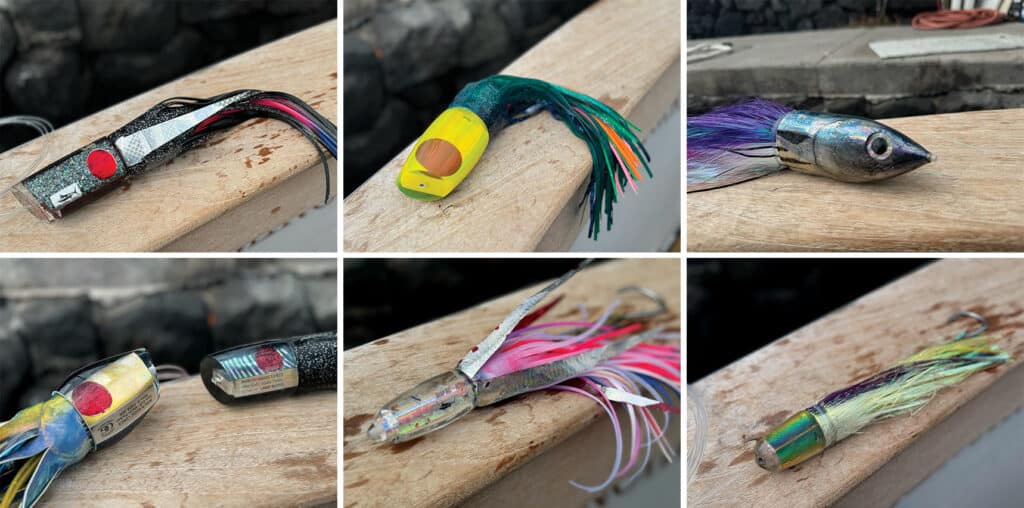
Niiyama agrees. “When machines replace human hands, craftsmanship and artistry can be replaced with copy and paste,” he says. “Art is a matter of perspective, though, and only the end user can dictate its worth.”
No matter the brand, style, shape or size of bait you choose to pull, just remember it arrived in your mailbox filled with positive energy. Learning how to manipulate that bait to swim exactly how you want is an art form all its own, one that can only be learned over time through trial and error. Treat your baits with the respect they deserve, and in so doing, add your own dose of mana to elicit that next blue marlin bite.